by Dr. Peter Harrop from IDTech
Lithium-ion is the winning type of rechargeable battery for the decade - there is almost a consensus. You can count about 150 manufacturers of these and IDTechEx has profiled nearly all of them. We expect 200 manufacturers of lithium-ion batteries soon, mainly because of the burgeoning number of Chinese companies making poor quality me-too-but-cheaper versions - notably the relatively easy-to-make small cylindrical versions such as the archetypal 18650 for laptops and small pouch versions for mobile phones. Then there are those that add basic flat-boxed "prismatic" versions for e-bikes but not much more. One million lithium-ion powered e-bikes were sold in Europe last year and China is starting to use them instead of the troublesome and polluting lead acid ones that the Chinese government seeks to control. Only 15% of lithium-ion battery manufacturers will continue to stay out of versions that propel vehicles.
There is almost a consensus that traction batteries for electric vehicles - hybrid and pure electric - will be the largest value market for lithium-ion batteries over the coming decade as a whole and certainly that electric vehicles will dominate use in later years by a big margin. IDTechEx projects a market for traction batteries in land and water vehicles plus aircraft of just under $60 billion in 2020 of which about 60% will be lithium-ion and 80% of those will be made by just four winning lithium-ion manufacturers.
For example, the number of mobile phones is becoming limited by the number of people in the world and it is not boosted by huge government support. The opposite is true of electric vehicles and they need the equivalent of thousands to tens of thousands of mobile phone batteries per vehicle.
The disagreement comes with just about everything else concerning lithium-ion batteries. What chemistry? IDTechEx has pointed out that most of the existing manufacturers and nearly all of the new manufacturers of lithium-ion batteries use lithium iron phosphate active cathodes because of advantages such as no materials subject to severe price hikes, low cost materials and easier patent position. They have good temperature performance that can reflect in greater safety though no lithium-ion cell is inherently safe and the first defender of safety is the Battery Management System BMS not the cell. Several recent fires and explosions have been related to something other than the cells.
The Japanese Institute for Information Technology notes that the leaders in sales of lithium-ion batteries for vehicles are in Japan (lowest material cost for the advanced materials) and Korea (fastest production lines), not China. We are told that the Japanese and Koreans, notably Panasonic including its Sanyo subsidiary, AESC and LGChem, base their success on ignoring lithium iron phosphate. This is partly because the primary driver of success of the potentially most popular electric vehicles in ten years time - pure electric and plug-in hybrid - is maximum all-electric range. There will be a huge take-off in sales when most people think the range of an affordable pure electric car is "adequate". Nobody knows that figure for widely acceptable range partly because there is almost no statistical correlation between how people respond to questionnaires and what they then do.
Certainly the main frontier of lithium-ion success is achieving affordably greater energy density meaning range. Any improvement creates sales but we do not know the tipping point. The Japanese Institute for Information Technology believes that if we look at the leaders not the mob, there is a trend from lithium manganese oxide active cathode to nickel cobalt manganese to reflect these market needs. This is an over-simplification of course: there are variants and alternatives even among the leaders.
There is near consensus that lithium-ion battery anodes have to get cleverer. That must result in them being more than a minor part of the cost: today they consist of little more than copper foil coated with carbon such as graphite. Disagreement reigns when it comes to routes and timescales, however. EnerDel, Altairnano and Toshiba have taken the lithium titanate route said to improve power density for fast regenerative braking and fast chargers at the roadside or bus depot. However, rather more organisations are now looking at silicon-based anodes and some are in the market though only in small batteries. It is argued that silicon can increase cycle life and even that vital energy density but does vanadium need to be involved? Nanotechnology? Graphene? Struggling for any agreement here, we can only say that most experts believe that the cleverer anode will cost more than its typically 14% of cost reported today but it will never cost as much as the cathode, with 35% of the total spend.
So how far will lithium-ion battery costs fall for that vital electric vehicle sector? A factor of three over the coming decade is commonly projected. Analyst Pike Research puts that at about $523 per kilowatt hour by 2017. However, the Nissan Leaf EV´s battery pack has been reported to be only $375 per kilowatt hour, while Tesla Motors CEO Elon Musk said recently that battery costs may fall to less than $200 per kilowatt hour "in the not-too-distant future."
Certainly, huge leaps in energy density, and potentially cost per kWh, have been reported just lately such as Envia Systems. In development, has broken the world´s record for energy density at 400 watt-hours per kilogram -- more than double today´s batteries. This matches the best of the so-called rechargeable lithium/lithium metal batteries that do not employ the lithium intercalation at the electrode that characterises lithium-ion. Such traction batteries are in use in modest quantities for military, aerospace, unmanned vehicle and car purposes. The small number of companies preparing them for major rollout sometimes claim they will replace lithium-ion traction batteries because of various advantages, not least energy density, where some feel that 600 kWh per kg will be achieved - maybe more. The IDTechEx analysis is in Electric Vehicle Traction Batteries 2012-2022 . These improvements will also hugely benefit the consumer electronics sector which is growing but being overtaken by the faster growing vehicle uses.
That has an echo in supercapacitors and the half-way house of the supercabattery (Asymmetric Electrochemical Double Layer Capacitor), notably the "lithium capacitor" which has one lithium-ion battery electrode. The developers of these, which now outnumber the number of developers of rechargeable lithium/lithium metal batteries, sometimes point to a theoretical 500-100 kWh per kg if the wonder drug graphene is employed. Just calculate the surface area! Unfortunately graphene, and its rival carbon nanotubes, turn out to need a lot more understanding, control and cost reduction in these applications. See the IDTechEx report Carbon Nanotubes and Graphene for Electronics Applications 2012-2022 .
Even before lithium capacitors become widely available and affordable, the original supercapacitors are replacing batteries in many applications where performance is more important than price. For more see the IDTechEx report, Electrochemical Double Layer Capacitors: Supercapacitors 2013-2023 .
The bottom line is that, if huge leaps in energy density can be achieved at an acceptable price, then a huge jump in electric vehicle sales may be achieved. Extrapolation forecasting is not enough. Think iPod. We recommend that you particularly track progress of lithium-ion batteries that do not use lithium iron phosphate cathodes, rechargeable lithium/lithium metal batteries such as lithium metal polymer and finally lithium capacitors in that respect, with advances in lithium-ion batteries likely to become mainstream first with that large increase in affordable energy density.
Meanwhile, the shakeout of the lithium-ion battery business is getting more dramatic. Few noticed when EnerSys, the world´s largest industrial battery manufacturer bought tiny ABSL on the tip of Scotland and redirected it away from traction batteries, aiming its various lithium-ion chemistries at military and aerospace applications not involving traction. Rather more have spotted the Chapter 11 demise of EnerDel (using NCM and LMO cathodes) then Valence Technology (using LFP cathodes) and now the big news that political football A123 Systems (using LFP cathodes) has only a few months money left having spent up to one billion dollars.
The primary reasons why these and at least fifty more in the queue will go under or exit will variously include poor quality, bad management, under investment and losing the race for affordable larger energy density: each is ticking at least some of those boxes. Of course some lithium-ion battery manufacturers can and are going niche. They address the special requirements of extremely cheap batteries for toys, the small minority of large-format, static applications in grid and uninterruptible power supplies where lithium-ion is the best solution, marine traction applications and so on. Valence Technologies seeks to continue in the business after Chapter 11 as does EnerDel and they will have to do some hard thinking about niches. The big boys will continue to slog it out with their multi-billion dollar investments and joint ventures. Include Samsung (keen on consumer) and Bosch (keen on automotive) in the SBLimotive traction battery venture that is landing quite a lot of business, if it stays together.
Many of the giants are reflecting the fact that more than half of the expenditure on electric vehicles lies beyond cars. This is well understood by Toyota - more than four times as big in electric vehicles as number two partly because it is world number one in pure electric and hybrid forklifts and near the top in hybrid electric buses. 176,000 hybrid and pure electric buses will be sold in 2022 according to IDTechEx report, Electric Buses and Taxis 2012-2022 . That is a huge amount of battery. Toyota´s Primearth Electric Vehicle Energy is making traction batteries and Toyota is out-patenting most of the so-called battery companies in energy storage for vehicles as revealed in the analysis of 100,000 patents by IDTechEx in Advanced Energy Storage Technologies: Patent Trends and Company Positioning .
Relevant Reports
Electric Vehicle Traction Batteries 2012-2022
www.IDTechEx.com/evtraction
Electrochemical Double Layer Capacitors: Supercapacitors 2013-2023
www.IDTechEx.com/EDLC
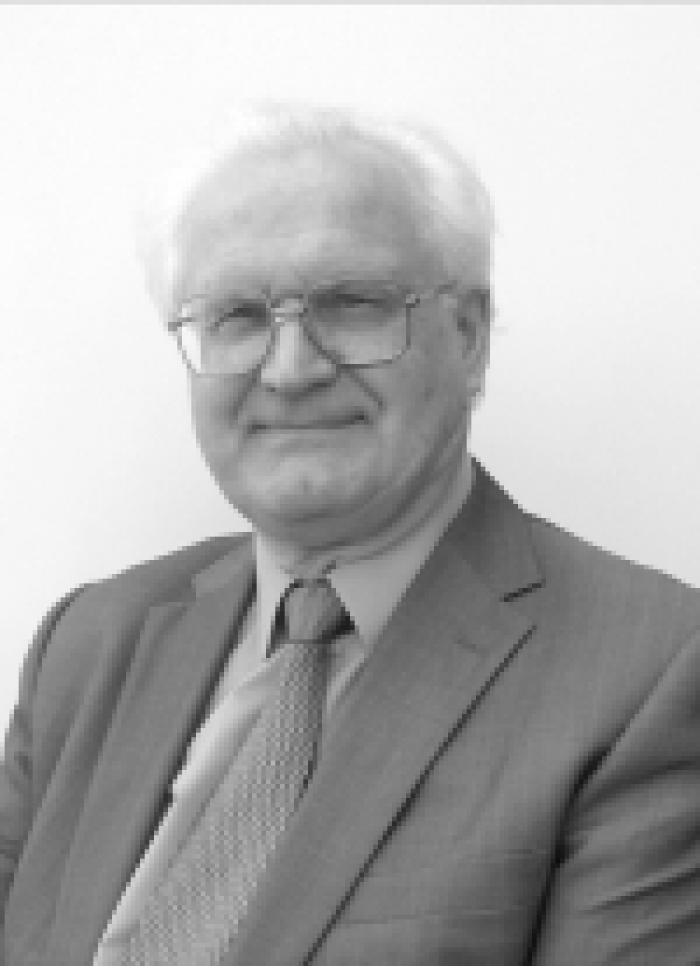
07 August 2012
Big disagreement on where lithium-ion batteries are headed
by