Innovative manufacturing technologies and the application of new materials characterize the production process for BMW i cars. Their production stands at the beginning of a value chain that is completely aligned with sustainability criteria. From the raw materials production to the energy-efficient vehicle operations and the recycling as the last step, the chosen approach makes a considerable contribution to the favorable overall life cycle assessment of the plug-in hybrid sports car BMW i8.
The BMW Group’s global lead in automotive engineering is demonstrated, among other things, in the industrial production of components made of carbon fiber reinforced plastics (CFRP). The development and production of both the combustion engine and the electric motor of the hybrid sports car are also carried out completely by the BMW Group.
The innovative vehicle architecture of the BMW i8 comprises two elements: the Life module, the passenger cell made of carbon fiber reinforced plastic (CFRP), and the aluminum Drive module, which incorporates the entire drivetrain and chassis technology. The LifeDrive concept and use of CFRP allows production times to be cut by half compared to those required for an equivalent car built along conventional lines. The process is less investment intensive as the high costs required for a conventional press shop and paint shop are no longer an issue and the Life and Drive modules can be manufactured alongside one another.
The BMW i production network comprises a plant in Moses Lake, Washington State, for the carbon fiber production and a plant in Wackersdorf for the processing into carbon fiber laminates. Both these facilities are operated by SGL Automotive Carbon Fibers (ACF), a joint venture set up by the BMW Group and the SGL Group. They are joined by the BMW Group’s own plants in Dingolfing, Landshut and Leipzig.
The carbon fiber plant in Moses Lake (USA) produces carbon fibers from a polyacrylonitrile-based thermoplastic textile fiber precursor. A complex multi-stage process eventually leaves a fiber that consists of virtually pure carbon with a stable graphite structure. This fiber is just seven microns (0.007 millimeters) thick. A human hair, by comparison, has a diameter of 50 microns. For automotive application, approximately 50,000 of these individual filaments are bundled and wound on reels, prior to further processing. Even in this first step, the production of carbon fibers at the plant in Moses Lake, WA, the power needed in production is solely sourced from fully renewable energy sources.
Processing into carbon fiber laminates in Wackersdorf. The fiber rovings produced in Moses Lake are sent to the Wackersdorf Innovation Park, for industrial processing into lightweight carbon fiber laminates. Carbon laminates with different fiber alignments are arranged into stacks made up of several layers and following various lines, before being cut to shape.
A preform mold is used to give the preformed carbon fiber stacks a stable, three-dimensional form. Several of these preformed blanks can then be joined to form a larger component. In this way CFRP can be used, for example, to produce body components with a large surface area that would be difficult – or significantly more expensive – to manufacture from aluminum or sheet steel. Preforming and preform joining are followed by the next stage in the process: high-pressure resin injection using Resin Transfer Molding (RTM). Here, liquid resin is injected into the preforms under high pressure. As the fibers and the resin bond, and in the subsequent hardening process, the material acquires the rigidity that is key to its outstanding qualities.
The CFRP presses work to precisely defined, specially developed time, pressure and temperature parameters until the resin and hardener are fully cross-linked and the resin is hard. This automated manufacturing process eliminates the need for the time-consuming hardening process in an oven, which would normally be required in manual CFRP production processes.
The CFRP process is no longer comparable with conventional sheet steel manufacturing. This industrialized manufacture of CFRP is extremely economical and makes the production of large CFRP composite components for the automotive industry a feasible proposition for the first time.
Even complex assemblies with many structural elements already integrated, such as an entire side frame for the BMW i8 Life module, are produced at the facility with a high level of automation. Additional processing stages include the finishing work, such as precise contour cutting and the insertion of remaining openings. This work is performed using a special waterjet cutting system and the bonding surfaces are then sandblasted before further processing. A conventional sheet steel side frame, by contrast, would have to be built up successively from several different inner and outer components.
The CFRP composite components are bonded together in the new body shop in Leipzig. This is where the basic structure of the Life module for the BMW i3 and the BMW i8 takes shape. There is no noise from bolting or riveting and no sparks from welding in the manufacturing process for a CFRP body. Instead, only the latest bonding technology is used, which is 100 per cent automated. In this unique, BMW-developed assembly process, the individual components are positioned at a precisely defined bond line gap in order to ensure the resulting joint is as strong as posible.
The outer skin of the BMW i8 is made entirely of thermoplastic; it is produced at the BMW site in Landshut. The weight of the plastic parts is around half that of sheet steel parts. Plastic also provides corrosion-free outer protection and requires less energy to manufacture, as well as being resistant to minor damage.
The futuristic shape of the BMW i8 prompted the specialists in the production area of Plastics Exterior to align the production technology accordingly. The size of the components and the complex design language, combined with the car’s gap size requirements, led to the model-specific development of the synthetic granules as well as to an alignment of the production, which is specifically geared toward meeting the BMW i8 requirements.
The bumpers, for instance, are given in their multi-tone paint coat in a highly specialized facility. This way a bi-color look can be achieved; at the same time, the weight is optimized significantly. Contrary to conventional models, not the complete body of the BMW i models is pained in a multi-stage process. Instead, the bumpers, front, rear and side parts are painted individually, which conserves resources. In the first step of the painting procedure, the entire bumpers are painted in black. Subsequently, the paint specialists at the Landshut site cover parts of the component with masking tape to ensure the separation of the different paint coats. In meticulous, delicate manual work, they cover the areas that are supposed to stay black. Then, the bumper goes through the paint facility again, this time for the second color, which is applied to all areas that are not masked. This paint process is handled by an innovative, automated robot facility. At the rear bumper, a tri-color design is achieved thanks to the additional mounting of a separately painted component; this additional color imparts a striking visual effect. While the conventional paint process coats the entire body-in-white in one piece, the assembly of separately painted attachment parts offers the possibility to create very special visual effects.
The structural parts of the of the BMW i8 Drive module built at BMW’s Dingolfing plant – the front axle carrier as well as the front and rear axle modules – consist of aluminum sheets and aluminum castings. An unrivalled facility concept with welding robots on a movable linear axle was developed in order to meet the construction-related challenges and to accommodate the large number of over 800 welding seams with a total length of more than 50 meters. The use of aluminum combines the advantages of lightweight construction with good crash performance and therefore contributes to the overall safety of the BMW i models.
A further important BMW i module produced in Dingolfing is the high-voltage battery. The production process starts with a ‘beginning-of-line’ test, in which the externally supplied lithium-ion cells undergo an initial performance check. The battery cells are then plasma-cleaned. Following this, the individual cells are clamped into modules, bonded and welded in a fully automated process.
Extensive BMW expertise goes into the special packaging and assembly of the battery. In all, the production process comprises 100 operations. After the battery cells have been packaged into modules, the assembly process begins. The modules are lifted one by one into an aluminum tray, then manually connected in series. The battery is designed in such a way that individual battery modules can be easily swapped for repair purposes.
Powertrain design has always been a key differentiator for the BMW brand. The BMW Group therefore decided to develop both the combustion engine and the electric motor for the plug-in hybrid sports car in-house. The 3-cylinder petrol engine with BMW TwinPower Turbo technology (231hp) is produced at BMW’s engine plant in Hams Hall (UK).
The BMW i8’s electric motor is produced at BMW’s Landshut plant. The BMW Group developed the 96 kW electric motor and drive electronics in-house. The internal components of the motor comprise an interior housing, a stator and a rotor. The stator, which forms the inner core of the motor, consists of around two kilometers of wound copper wire. What makes the BMW i8 motor so special is that, unlike other electric motors in the same power class, this motor is very small and compact due to the specially configured winding of the copper wiring. This results in further weight and space savings. Before the stator is fitted in the interior housing, it receives a thin coating of resin. Assembly of the stator, rotor, interior and exterior housing now takes place, the interior housing first having been heated to a temperature of around 150 degrees Celsius so that it expands slightly. This task requires maximum precision; the stator and the rotor have to fit together perfectly to ensure that later the motor runs smoothly.
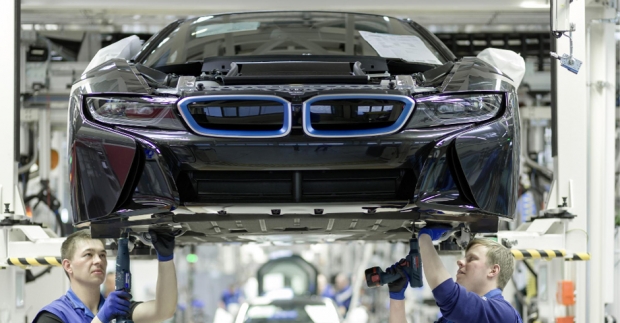
00 00 0000
BMW i8
by
V. Christian Manz
You can support me and my articles by donating the amount you want.
I will be very grateful.
I will be very grateful.